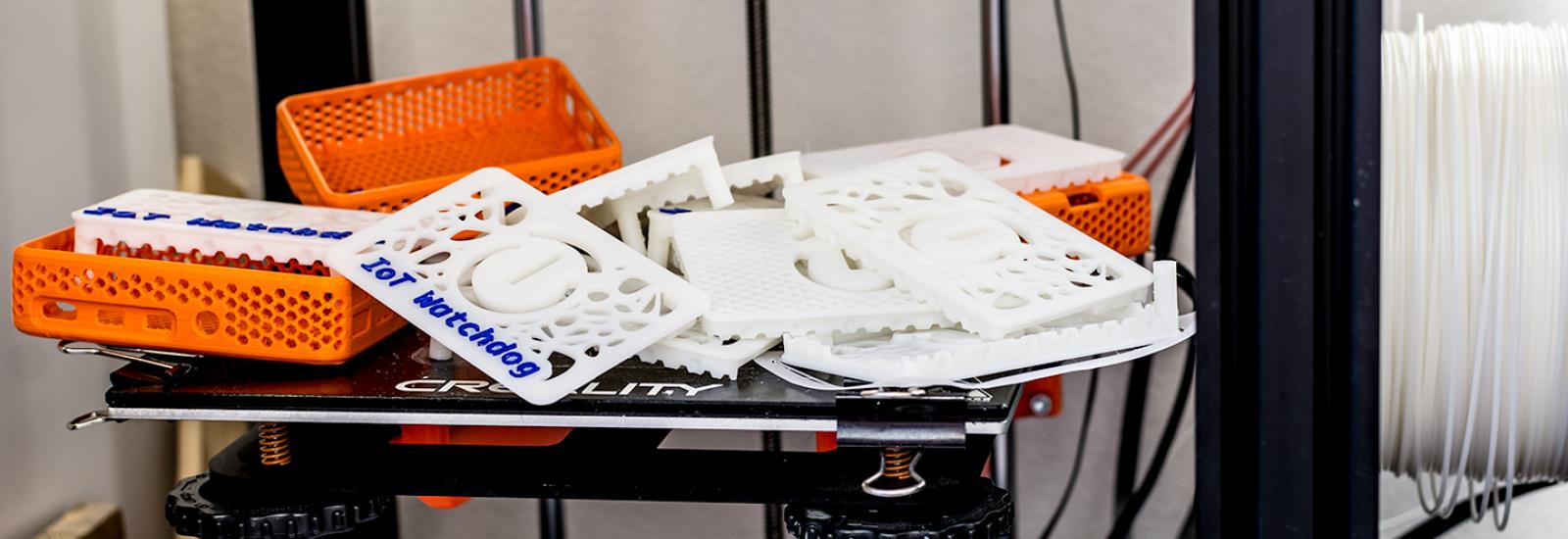
Förderjahr 2019 / Project Call #14 / ProjektID: 4430 / Projekt: IoT-WatchDog
Damit der IoT-Watchdog-Raspberry Pi nicht ungeschützt bleibt, braucht er ein Gehäuse. Um die Sache einfacher zum Nachbauen zu machen liefern wir einen Vorschlag für ein Gehäuse, das wir gefunden, getestet und für den IoT Watchdog angepasst haben.
Anforderungen
Zu Beginn waren, wie bei jedem Projekt, auch beim Design des Gehäuses die Anforderungen im Fokus:
- Nachdem es sich bei dem Netidee-Projekt in erster Linie um eine Software-Implementierung handelt, sollten für das Gehäusedesign nicht übermäßig viel Ressourcen verwendet werden. Wir entschieden uns daher zuerst nach einem fertigen Gehäusemodell im Internet Ausschau zu halten und dieses bei Bedarf zu modifizieren.
- Wir benötigen nur eine geringe Anzahl an Prototypen, demnach fiel die Entscheidung die Gehäuse am eigenen 3D-Drucker zu fertigen.
- Für gute Wartbarkeit - es handelt sich schließlich um einen Prototypen - soll das Gehäuse möglichst ohne Werkzeug öffen- und schließbar sein, sowie nach Möglichkeit ohne Schrauben zusammenhalten.
- Der Raspi4 braucht eine gute Lüftung, also legten wir Wert auf gute passive Ventilation (bei Bedarf kann ein Lüfter hinzugefügt werden).
- Stabile Konstruktion und Material (ist bei 3D-Druckteilen besonders wichtig)
- Zumindest halbwegs schön.
- Individualisiert, da wir die Situation sehr gut kennen, dass schnell eine Menge Raspis vorhanden ist und man nicht mehr weiß welcher welche Aufgabe hat.
Websuche
Die erste Suche brachte recht schnell einen guten Treffer, also machten wir uns gleich an Drucktests und die Anpassungen.
Das Gehäuse basiert auf einem Design von Carter Multz (Carter hat die Designs mittlerweile vom Netz genommen, er hat mir geschrieben, dass er an einer eigenen Website arbeitet, auf der er seine Open-Source-Arbeiten veröffentlichen will).
Modifikationen
Die Quelldateien waren, 3D-Community-spezifisch, nur als .stl und sogar als .gcode verfügbar, was eine weitere Bearbeitung leider sehr schwierig macht. Das Gehäuse besteht grundsätzlich aus einem Unterteil (Basis) und einem Oberteil (Deckel).
Unterteil (Basis)
Die Basis ist fertig und gut so wie sie ist, daher wird sie so gedruckt.
Material
Als Material haben wir uns für 3DJakes niceABS entschieden, weil wir damit schon gute Erfahrungen haben, es sehr haltbar und stabil, aber gleichzeitig gut druckbar ist. Die Schrumpfrate (shrinking) hält sich in Grenzen, die Layerhaftung ist sehr gut. Es ist das stabilste Material mit dem wir bisher gearbeitet haben.
Unser Drucker ist "open frame", das heißt er hat kein Gehäuse und ist daher, speziell bei ABS, anfällig für "Warping". Das bedeutet, dass sich die oberen Schichten beim Abkühlen zusammenziehen, während die unteren Schichten durch das 80°C warme Heizbett auf Temperatur bleiben. Das Druckteil verzieht sich so und kann sich in den Randbereichen vom Druckbett ablösen. Optimalerweise soll bei Materialien wie ABS der gesamte Bauraum des Druckers eine konstante Temperatur haben, die der des Druckbetts entspricht, und erst nach Beendigung des Druckvorganges gleichmäßig abgekühlt werden. Diesen Luxus eines temperierten Bauraumes haben wir leider noch nicht.
Oberteil (Deckel)
- Der Deckel musste in zwei Teile geteilt werden, wobei der eine Teil die genaue Passung für den Unterteil darstellt und unberührt blieb. Den obersten Teil, den eigentlichen Deckel, haben wir modifiziert.
- Die Mesh-Geometrie kann in vielen verschiedenen Programmen getrennt werden, wir haben einen erfolgreichen Versuch in Meshmixer gewagt.
- In Fusion 360 wurde die Passung importiert und vermessen, danach der neue Deckel gezeichnet.
- Zuletzt wurden die beiden Teile des Deckels wieder in Meshmixer importiert und als zusammenhängendes Mesh im .stl-Format exportiert. Eine Verschmelzung der beiden Teile ist dabei nicht nötig. Die Auflösung der beiden Meshes ist unterschiedlich und die Vertices sind an unterschiedlichen Positioen. In Meshmixer ist eine "Verschmelzung" zwar möglich, der Vorgang führt aber zu Deformationen an der "Schweißstelle".
- Als Slicer diente Ultimate Cura, gedruckt wurde bei Prototypen und Tests meistens direkt über USB.
- Im ersten Schritt haben wir auch beim Deckel die hexagonale Form der Ausstanzungen vom Originaldesign übernommen, im Verlauf beschlossen wir aber eine andere Form zu wählen. Aktueller Stand sind Öffnungen, die Voroni-Kurven entsprechen (z.B. mit Voroni Sketch Generator). Zu beachten ist, dass die Stege zwischen den "Löchern" nicht zu schmal gewählt werden, da es erstens schwerer druckbar ist und zweitens zu einer geringeren Festigkeit des Deckels führt. Der Designer des Originalgehäuses hat schon Gefallen an der Voroni-Idee gezeigt.
- In der Mitte des Deckels ist das "UnravelTEC" Firmenlogo eingelassen, das auf der Innenseite des Deckels verstärkt wurde um eine ausreichende Stabilität zu gewährleisten.
- Später ist der "IoT-Schriftzug" hinzugekommen, wir haben uns für ein kräftiges Blau entschieden, da es gut mit der orangen Basis kontrastiert und auch in unseren Firmenfarben ähnlich vorkommt. Natürlich gibt es unsere Firmenfarben (noch) nicht als Filament ;-)
- Blaues Filament ist in unserem Fundus vorhanden, wenngleich leider nur als PLA. Wir haben uns schon gefragt welche Herausforderungen die Kombination mehrerer Materialien bringen mag, zudem trägt der Schriftzug nicht viel zur mechanischen Stabilität bei, also wagten wir den Versuch. Aus heutiger Sicht führt dieser Materialmix zu keinen Problemen.
3D-Druck
Die ersten Testdrucke erfolgten mit niceABS in "Natur". Nachdem uns das Material zusagte, die eine Farbe aber etwas langweilig ist haben wir den Unterteil in Orange, den Deckel in "Natur"-Weiß und den "IoT Watchdog"-Schriftzug in ecoPLA Blau gedruckt.
Herausforderungen, technische Details
- Basis: Ist gut druckbar, die hexagonalen Ausnehmungen drucken mit 0,4mm Nozzle nicht immer 100%ig sauber, aber annehmbar.
- Deckel: Annehmbare Druck-Qualität mit 0,4mm Düse, die Ausstanzungen für den Schriftzug könnten aber eine etwas höhere Auflösung vertragen. Mit 0,2mm Nozzle ist es sehr viel besser, was aber besonders beim Deckel, zu einer langen Druckzeit führt. Ein Test mit 0,3mm Nozzle ist erfolgreich verlaufen, so haben wir einen guten Kompromiss zwischen Detail und Druckzeit erreicht.
- Wichtig ist für diese Passungen einerseits eine ausreichende "Clearance" der Bauteile (Abstand zwischen den zu kombinierenden Bauteilen, 0,3mm in unserem Fall). Bei PLA (und PETG) verwenden wir ausserdem im Slicer noch die Einstellung "Horizontal Expansion" um der Expansion beim Drucken entgegenzuwirken (-0,1mm hat sich bei uns bewährt). Wir drucken bei funktionalen Teilen mit eher höheren Flussraten und Temperaturen um eine gute Layerhaftung zu erreichen. Die Zufuhr von Filament (Extruder) ist natürlich kalibriert.
- Bei ABS ist die letzte Korrektur wegen der materialspezifischen höheren Schrumpfrate nicht mehr nötig.
- Drucktemperaturen:
- PLA: Nozzle: 195-200°C, Bett: 60°C
- niceABS: Nozzle: 250°C, Bett: 80°C (behelfsmäßige teilweise Einhausung aus Karton gegen Zugluft ergibt eine Bauraumtemperatur von ca. 40-45°C)
- Druckgeschwindigkeit: 50-60mm/s für Produktion, 80-100mm/s für Tests
- Betthaftung: PLA: Skirt, ABS: Brim, Adheasy Spray oder PrintaFix Basic
- Druckbett: Creality Tempered Glas Bett
Conclusio und Ausblick
Die Erfahrung aus dem IoT-Watchdog Gehäuse zeigt wieder einmal, dass es bei jedem neuen Material ein paar Versuche braucht, aber schlussendlich sind wir hier mit dem Ergebnis sehr zufrieden. Eine Massenfertigung ist mit dieser Methode nicht möglich, die Daten können aber durchaus als Basis für andere Produktionsprozesse, wie z.B. Spritzguss, dienen.
Appendix
Der Weg zum Gehäuse in Bildern
3D-Rendering
3D-Dateien
Die Druckdateien unseres 3D-Druck-Gehäusedeckels könnt ihr auf https://github.com/IoT-Watchdog/3d-designs herunterladen.